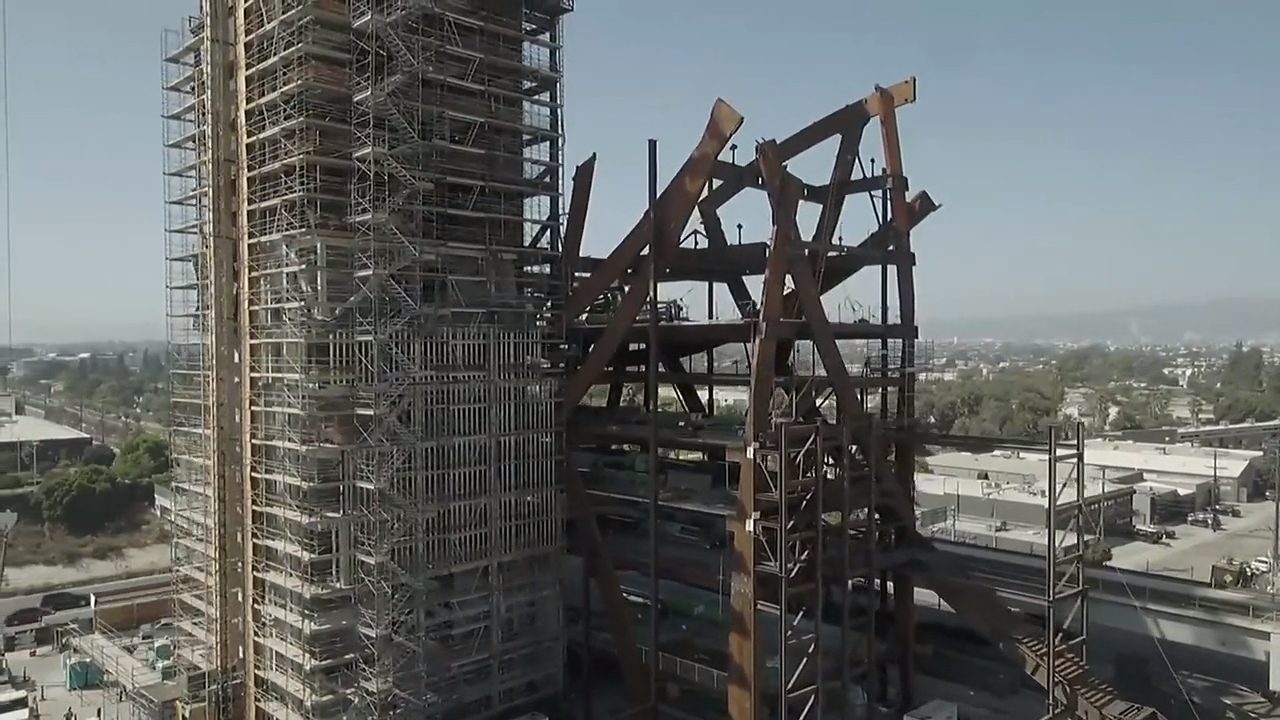
Location
Los Angeles, CA
Owner
Samitaur Constructs
Architect
Eric Owen Moss Architects (EOMA)
Project Size
180,548 SF
ViewMeet LA’s First Exoskeleton Building: The (W)rapper
MATT’s Team Works with EOMA and Arup to Build the (W)rapper, LA’s First Exoskeleton Building
How do you build a 17-story office building with no central columns? It’s hard enough to wrap one’s mind around the idea, let alone to wrap an actual steel-frame exoskeleton around a structure outfitted with floor-to-ceiling glass windows. But that’s exactly what the (W)rapper’s ingenious design calls for. Over two decades in the making, the bold concept came to life through the vision of Eric Owen Moss Architects. MATT’s team came into the picture during preconstruction to finalize the engineering, permitting process, budget, scope and buyout with trades before breaking ground.
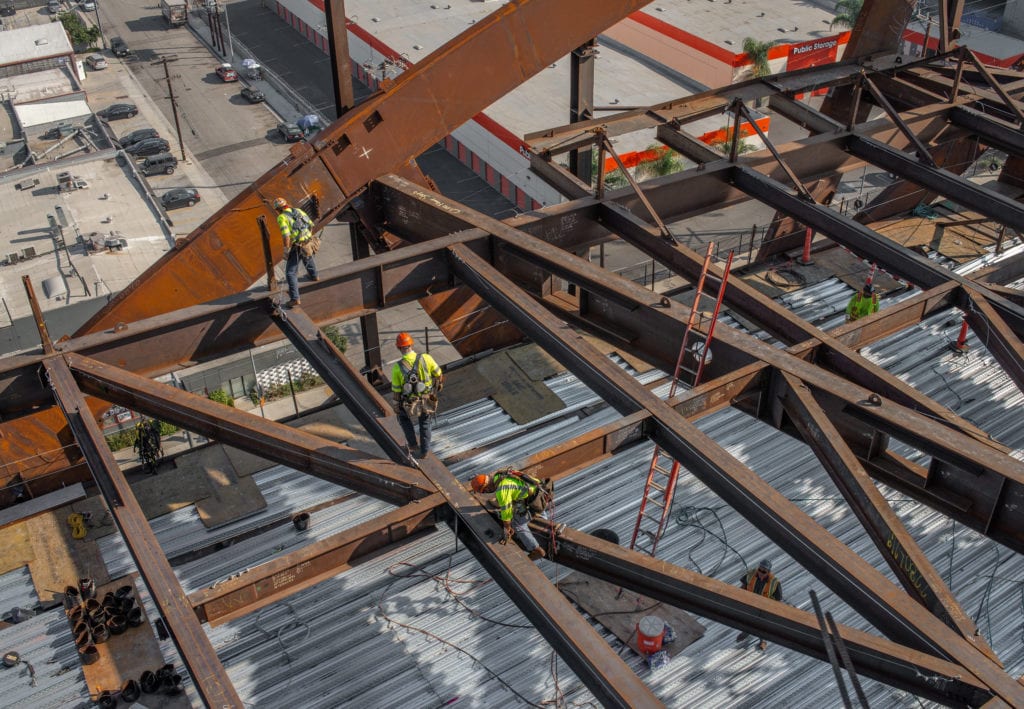
How an Exoskeletal Support Structure Works
Normally, a building relies on conventional internal structural elements, such as column and beam framing, that transmit weight and load through compression. What makes the architectural intention behind the (W)rapper novel in LA is the proposal to support from the outside-in rather than inside-out. The outer steel framing bands, also known as the tower’s exoskeleton, serve as external columns. Eight bands run all the way down and connect to isolator nodes which sit on base isolation, which in turn rest atop concrete pilasters. Engineers and architects spent years calculating the possibilities and came up with a design that would leverage gravity and lateral and seismic loads. The bands wrap around the building neither strictly vertically nor horizontally, but in their own abstract way, acting as their own structural frame. This lack of consistent patterning on the façade adds to the constructability challenge and also to its striking uniqueness.
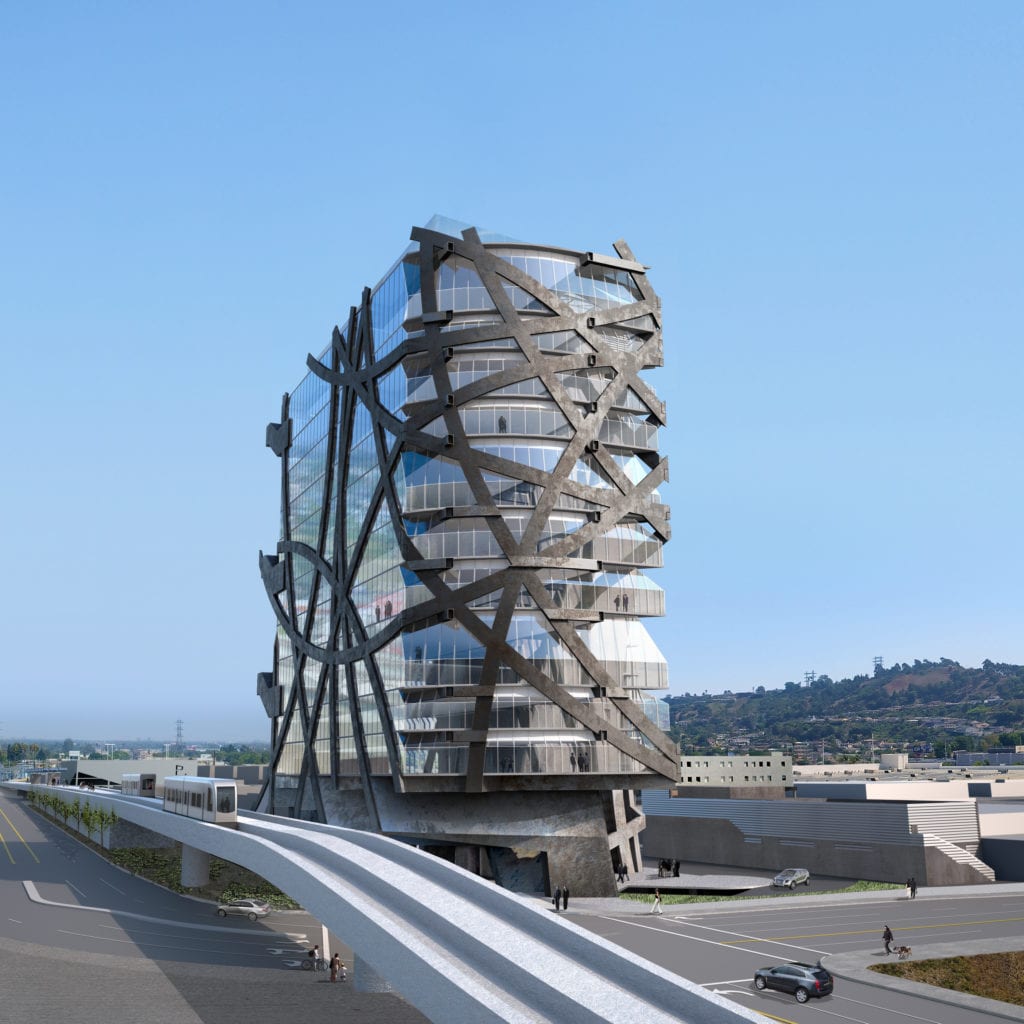
Split into two discrete sections but still one distinct building, the (W)rapper will consist of a 17-level ‘core’ area relying on traditional beams, columns and a steel plate shear wall and a 16-level ‘tower’ area, which will stand without internal columns. The core holds the restrooms, mechanical shafts, elevators and electrical rooms, while the tower contains office space. The core is being built independently of the tower, set to be completed before its counterpart. In fact, the core must be complete in order for the tower to go up due to the nature of the tower’s framing system. Once the tower and core are both finished, they will stand as one building and be self-supporting.
Balancing a Tight Order Of Operations
Tackling a challenge of this magnitude and rarity requires a careful plan of execution that factors every stage into the sequencing. To kick off that long and complex process, the team first demolished and excavated the site. Next came an elaborate shoring effort, followed by an intensive overnight pour of the structure’s mat foundation. (See the video here). Once the foundation had cured, the team began work on two levels of below-grade parking.
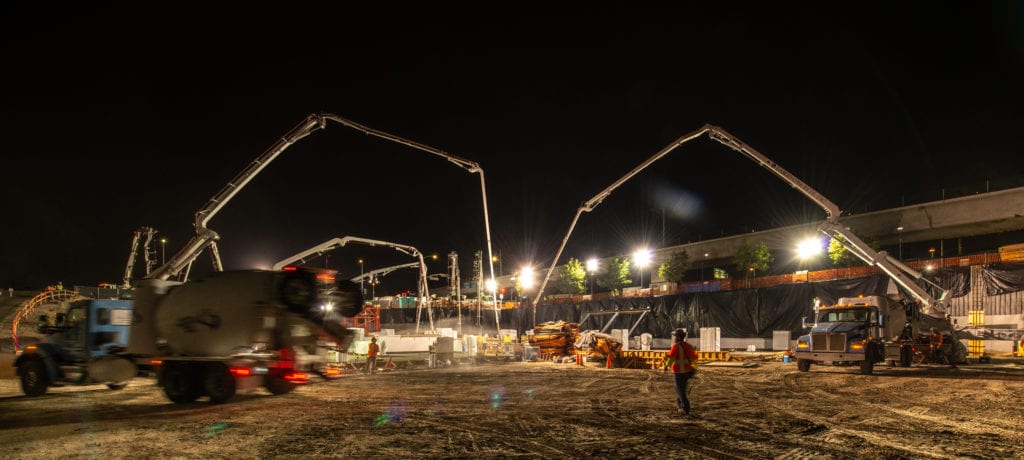
The tower will continue to rise alongside its supporting structural steel bands. Floor framing, chords, girders and supplemental end fill beams all get fixed into place at that time as well. The floor framing chord beams run from the core to the steel bands and support those bands, meaning they must be set in place in sequence with the bands. The team is working on two floors at a time in the tower. As the bands go up, the floor framing goes in and gets welded, after which comes a metal decking, a concrete pour, and then on to the next level.
An Interplay Of Shoring and Steel Bands
Although the overall shoring scheme for the parking garage relies on typical soldier beams and lagging, the crew had to set up a temporary shoring component to erect the structural steel bands. They followed a detailed procedure to install each piece, band by band, beam by beam. A series of wide flange temporary columns went up around the perimeter of the tower, placed strategically just outside where the bands would go, to act as temporary shoring. Each band gets tied off to a temporary column, all the way to the top. Once the structure is complete and the steel is 100% erected and welded, the structure can support itself. At that point, the team will begin an equally involved de-shoring process, disconnecting the bands from the temporary outer columns.
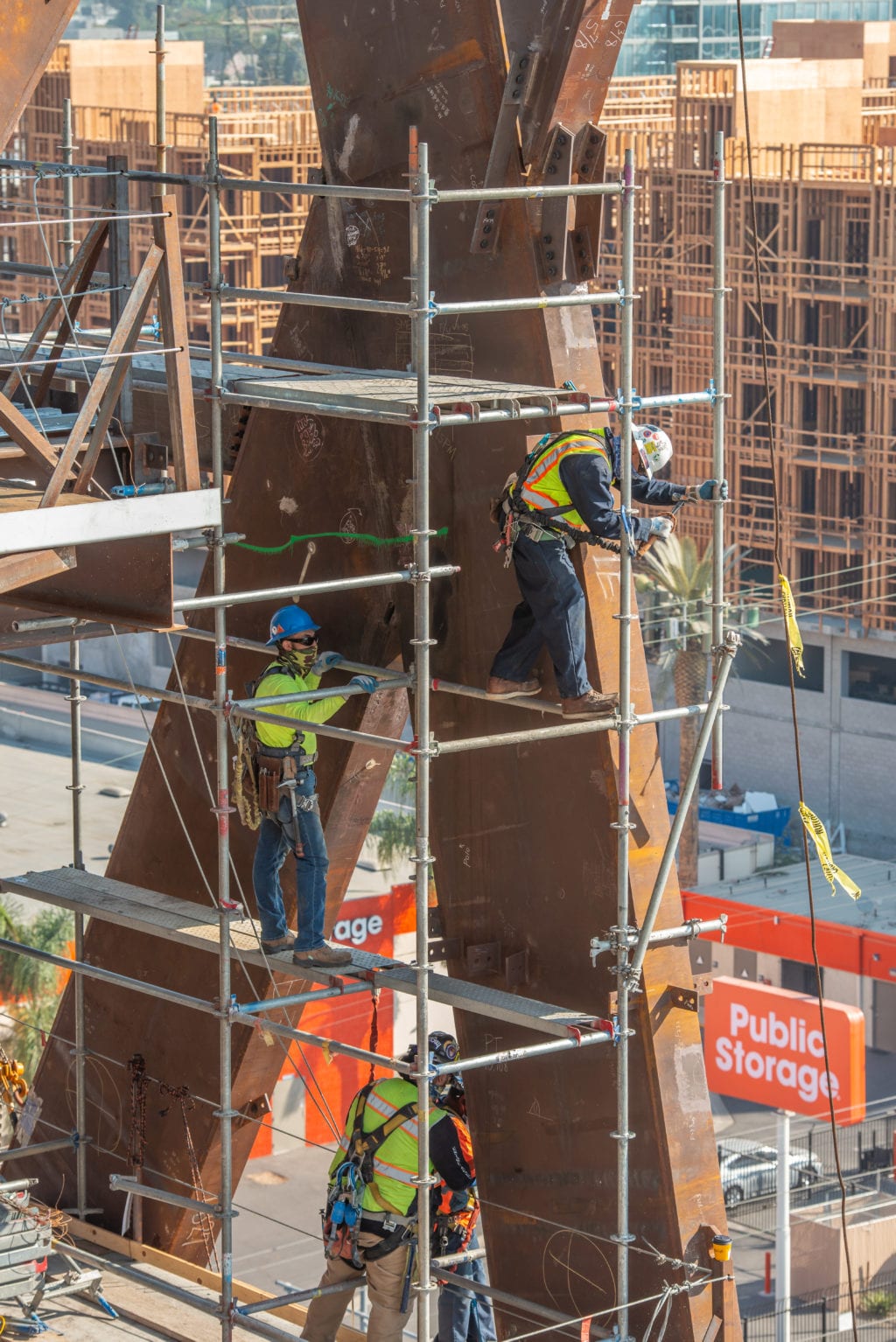
The structural steel bands are all fabricated in China to the exact length and size specifications stipulated by the engineers and architects. Each band is unique in shape, size and weight, adding to the complexity of the challenge ahead. A total of six shipments are being delivered to California by sea, unloaded from the port and stored in a Long Beach shipping yard. As the team prepares to erect the next sequence of bands, they bring the material in from Long Beach. A massive tower crane on site hoists the fabricated material into place. Weighing in anywhere between 40,000 and 100,000 pounds, these pieces demand care and precision in handling. After they’re moved to their designated positions on the site, temporary erection bolts set the steel in place, followed by welding. Over 26,000 person-hours of welding has been factored into the schedule, including a Monday to Saturday swing shift from 4:30 pm to 2 am.
One Of a Kind Challenge, One Of a Kind Opportunity
MATT has handled a number of projects with tricky façades in the past, such as the overhaul of the Petersen Automotive Museum. But the Petersen’s iconic, racing silver ribbons are architectural and not structural. Kevin Pitzer, Senior Project Manager at MATT Construction and on the (W)rapper site, shared that he’s “worked on unique and challenging projects, but this is one of a kind. I haven’t seen anything like this in Los Angeles.” Of the few other structures in the world that also rely on exoskeletal support, this is the only one with no clear pattern to the façade, ratcheting up the level of difficulty in the preconstruction and prefabrication stages. The (W)rapper project has been an exciting innovation in the world of construction for everyone on board, and the team looks forward to stepping away and seeing the building stand on its own from the outside.
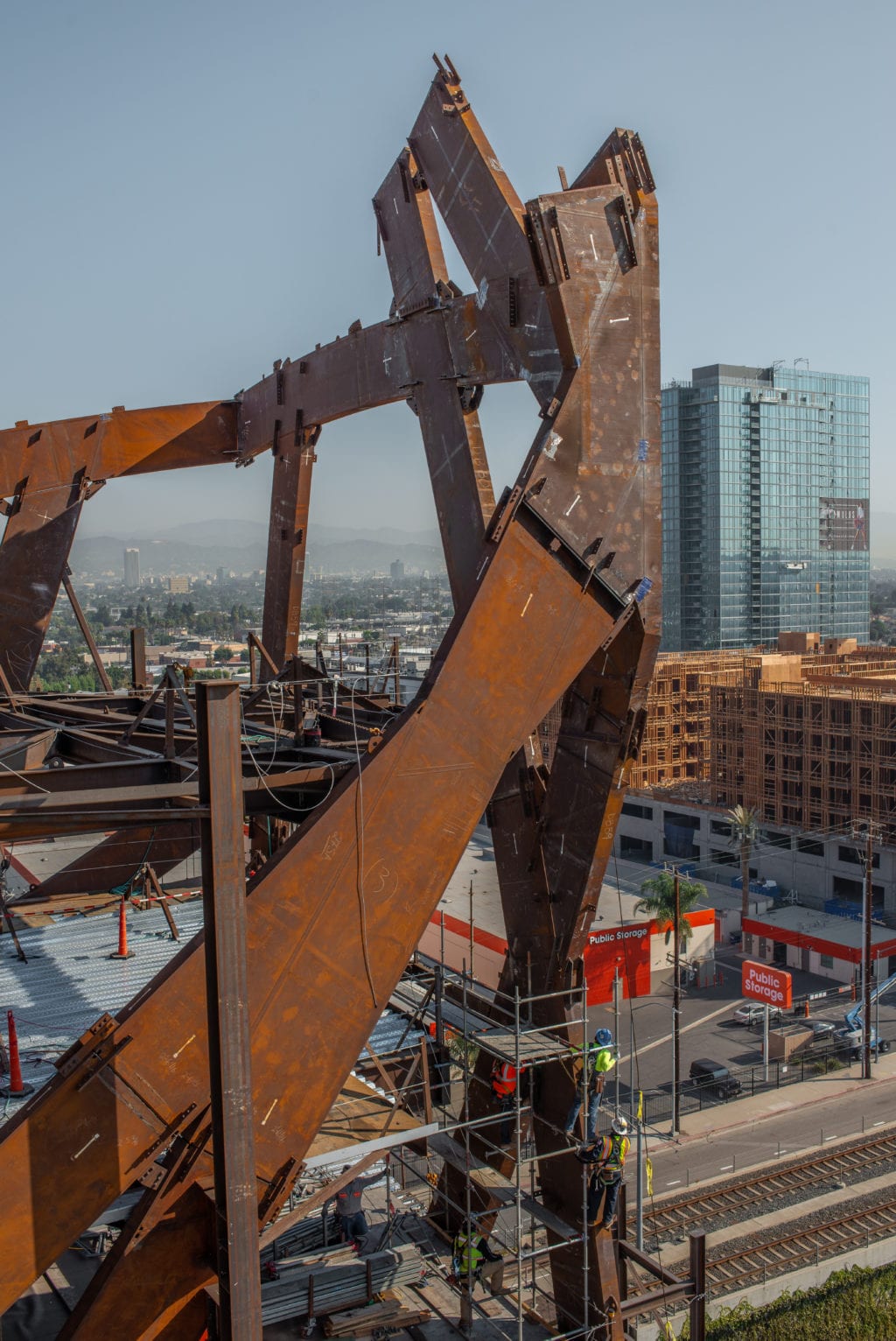